Services
Effective - Simple - Practical
SYSTEMATIC AND IN-CONTROL
We work with clients, creating an atmosphere of trust and respect while providing solutions that strengthen their existing operating management systems.
Without appropriate systems, processes and standards as foundation blocks, process safety has a "hollow" meaning and may be referenced as a PR stunt or "window dressing". Equipment design and installation must be "inherently" safe to have a robustly safe work environment. An inherently safe design seeks to either eliminate the hazard, reduce severity and reduce likelihood of an undesirable event. Without this framework, personal protective safety does little to protect personnel from fatalities or life changing injuries.
We approach risk management from systems perspective. The Bowtie methodology provides a visual blueprint where preventative barriers can be clearly defined and communicated. Escalation barriers can also be visually articulated in the event that all in-line preventative barriers fail, systems can be put in place to prevent escalation of the undesirable event.
Our expertise is based on 40 years of working experience in the upstream oil and gas industry. The foundation principles of the Bowtie methodology are transferable and applicable to any undesirable event regardless of the industry or scenario.
Take a look below at the engagement process and get in touch for a free consultation to learn more.
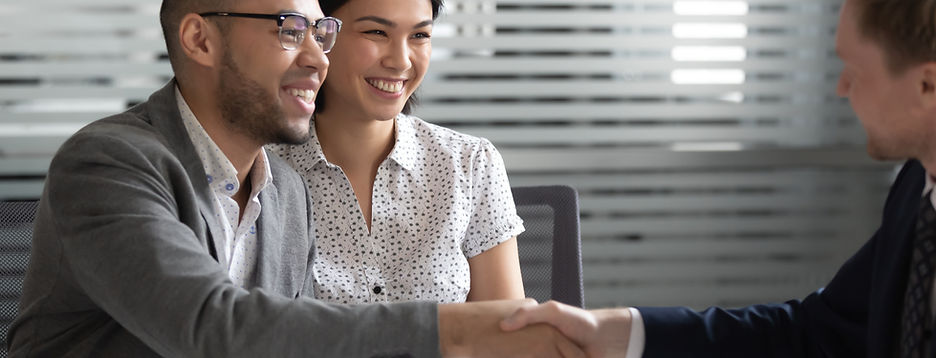
Creating the Blueprint
Without a blueprint, measures or actions taken by any well intentioned operator may be "hit and miss". There may be multiple scenarios associated with a single undesirable event. All these should be investigated. Without a blueprint, it is more likely the some key threats and scenarios that cause the undesired event may be overlooked. Consequently critical systems, equipment or activities may be inadvertently omitted.
An open mind set is required throughout the entire process of mapping this blueprint.Think of this blueprint as a "roadmap" that will help define the required systems and processes that need to be in place. With a blueprint, preventative and escalation measures can be easily added or modified to strengthen the overall safety systems on a continuous basis.
The first step is the identification of the hazards. The top events associated with each hazard needs to be defined. The scope of work can then be defined based on the events that the blueprint will address. We call this the "APPRAISE" stage.
Below is a list of some of the "TOP EVENTS" for management in the upstream oil and gas operations.
Common Top Events
-
Loss of well control during well construction operations
-
Loss of well control during well intervention operations
-
Loss of well control during well production operations
There may be scenarios where other precursory events may be caused by threats but do not escalate into a top event. These can be identified in the APPRAISE stage as well e.g. A rig collapse may lead to a fatality without resulting in a loss of well control.
What to expect
Building the Blueprint - the DEFINE stage
Once the APPRAISE stage has been completed, work can be initiated to build the blueprint for each undesirable event
This stage involves:
-
Creating the scenarios for each causal threat
-
Identification of preventative barriers for each threat
-
Classification of each preventive barrier - safeguards nay be passive, active or procedural
-
Defining the strength of each preventative barrier based on classification
-
Identification of escalation factors and associated barriers
-
Declaration of risk scenarios not investigated
Systems Gap Analysis
This work stage compares the blueprint with systems, processes, standards and procedures that are already in place. System gaps are identified. These may be related to critical equipment or critical tasks.
Examples of gaps:
-
The equipment design is not inherently safe
-
An equipment's maintenance program may exist but its maintenance routines and inspection findings may be manually managed by a human
-
Standards for inspection and maintenance requirements may not exist
-
Operating and Maintenance procedures exist but are flawed
-
No oversight of competency of contractor maintenance technicians
Systems Implementation
This stage of the process may be the most challenging as it may involve capital costs and time. It all about executing key actions from the gap analysis. Generally this stage is executed in-house but can be supported with consulting expertise. Activities may involve:
-
Modifications of equipment installation
-
Installation of new technology enhanced equipment
-
Acquisition and implementation of software applications in management processes
-
Review and modification of activity work flows with decision points and authority (RAPID) designation
-
Development of documents
-
Operating Management Strategies
-
Equipment maintenance strategies
-
Standards and Technical Practices
-
Operations and maintenance procedures
-
System Review
A periodic review may be required in most cases. This may include:
-
Conformance and gap assessment
-
Assessment of strength and effectiveness of barriers
-
Action plan for continuous improvement
Check out our Blog for more content
How we work
Clients have the option to engage our services based on each stage in the process.
APPRAISE Stage
This stage is critical in any project scope. It provides a broad work scope and feeds an agreed Terms of reference.
The terms of reference defines the desired outcomes and establishes the boundaries of the investigation.
It is the basis for the contractual terms.
DEFINE Stage
This is the stage where the Blueprint Is developed.
EXECUTE Stage
This stage involves 2 parts
-
Systems gap analysis
-
Systems implementation
REVIEW Stage
This stage is generally a periodic review geared to learning from what has been implemented and a continuous improvement cycle.
Contact us to for a free consultation to discuss your needs!